Battery-up: Climate change is essentially an energy challenge
Rechargeable batteries to store the energy of renewables and electrify our transportation promise to be a critical step in fighting climate change.
Now everyone knows about the wonderful lithium-ion (Li-ion) batteries, the workhorse of today’s battery technologies.
Few, however, are aware of the rising environmental concerns regarding the production of this seriously mineral-intensive battery technology – concerns that should be addressed urgently, otherwise the net impact of batteries won’t be as positive as needed to combat climate change.
When we think of Li-ion batteries, lithium comes to mind first, as it should – it’s the indispensable element of the battery. But do you know about the other silent partners, the critical battery minerals nickel, cobalt, and graphite? Right now, these commodities and Li-ion technology go together like Bonnie and Clyde.
Lithium
“Salt in the salad”, as Elon Musk nicely put it, refers to the small amount of lithium in the Li-ion battery, no more than 2-3%. So, as opposed to the rare earth metals nickel and cobalt, with an already foreseen scarcity, lithium supply isn’t an issue.
However, mining for lithium endangers it all – the air, the land, and the water. Estimates suggest producing one ton of lithium requires almost two million litres of groundwater and releases 15 tonnes of carbon dioxide.
Nickel
“Our Li-ion batteries should be called nickel-graphite,” Musk suggested in 2016, given that the main ingredient of the positive electrode in Tesla batteries is nickel.
Mining for nickel is an extremely energy and water-intensive process. The carbon footprint of nickel production is also estimated to be somewhere between 8.1 to 13 tonnes of carbon dioxide per tonne of the final nickel product.
Moreover, mining for nickel-rich ores, their crushing and transportation can introduce large amounts of toxic dust in the air, containing high concentrations of potentially toxic metals – nickel itself, copper, cobalt, and chromium.
Cobalt
“We think we can get cobalt to almost nothing,” Musk said in 2018. The idea of cobalt-free batteries is undoubtedly attractive. However, many battery manufacturers, including Apple, believe that at least small amounts of cobalt are critical in the battery’s positive electrode. Cobalt boosts the battery life by maintaining the integrity of the positive electrode, improves safety, and increases the rate at which the power is delivered.
Cobalt appears to be the costliest of all – price-wise, environmentally, and human-wise. The mineral is already expensive, and the expected shortage as early as 2025 drives surges in cobalt prices.
Read more: Turning solar panels that are past their use-by date into renewable opportunities
The environmental cost of its production is also on the rise. The total CO₂ emissions output of cobalt production in 2021 is approximately 1.6Mt, and is expected to nearly double to 3.0Mt by 2030, with most battery manufacturers keen on keeping cobalt in the battery.
The human cost regarding cobalt mining is also no news to anyone – where tens of thousands of children work in extremely harsh conditions in Congo, home to more than 50% of the world’s cobalt reserves. The radioactive particle-containing dust from extraction is linked to birth defects, respiratory diseases, and cancer.
Graphite
In the early 1970s, the 2010 Nobel Prize winner Stanley Whittingham replaced the highly reactive lithium metal with graphite in the negative electrode of lithium battery, and that’s how the reliable, long-lasting lithium-ion technology was born.
Graphite hasn’t experienced the price surges that the other critical battery minerals have seen throughout the years, mainly because its consumption in the steel industry drives the price of the material. However, with EV production booming, and considering battery manufacturing requires 10 to 15 times more graphite than lithium, monitoring the climate change impact of graphite mining is becoming more and more relevant.
In mining for graphite, the dust generated from explosives can blow fine particles into the atmosphere, causing health problems and contaminating the land.
The production of battery-grade graphite, in particular synthetic graphite, is highly energy-intensive. With nearly all the battery-grade graphite being sourced from China, the operators seek the cheapest power source, coal, causing high carbon dioxide emissions.
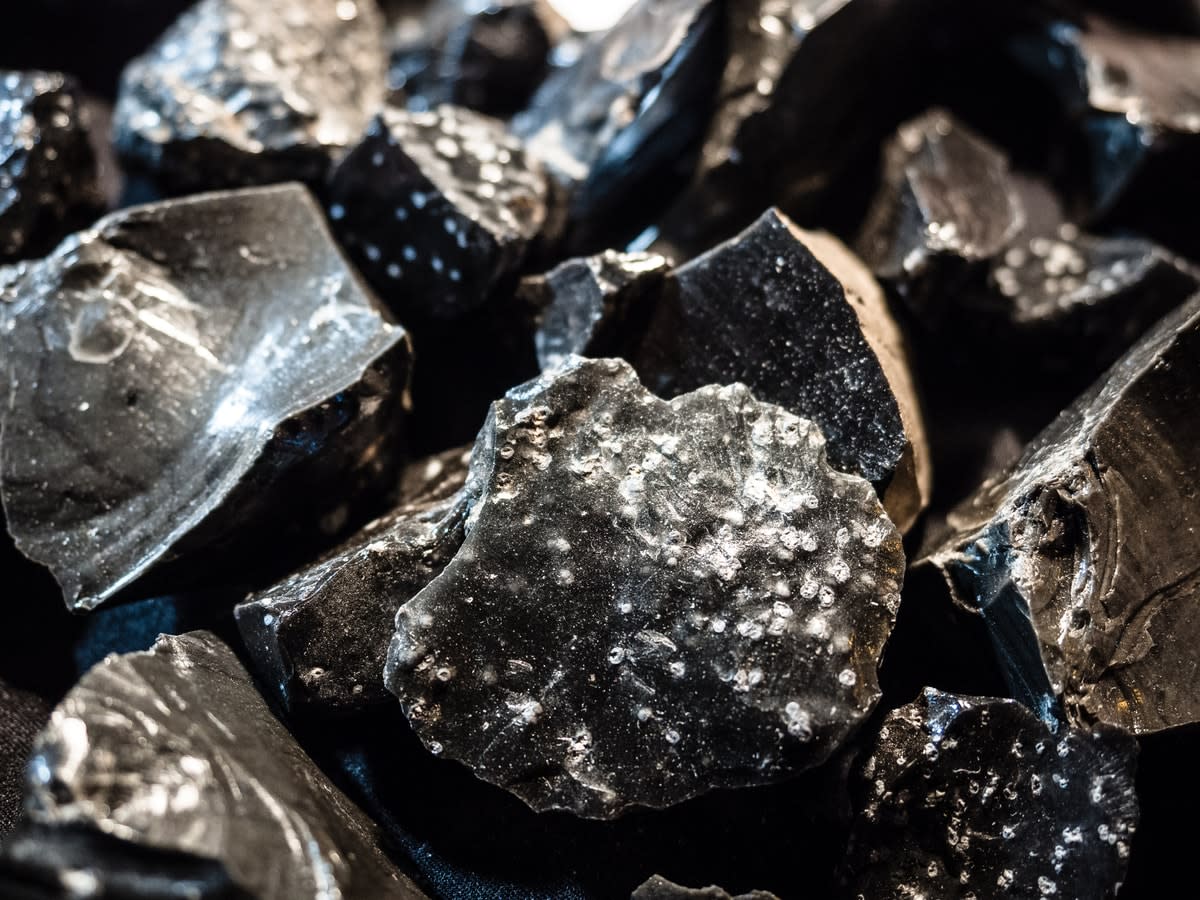
Striking the balance in battery production
Now, climate-responsible mining, waste prevention of used batteries, and moving towards greener battery chemistries will help with accelerating the electrification of our world, while ensuring the battery production is managed in a way that minimises the environmental and climate footprint.
Innovative and responsible mining
Traditional mining of all the critical battery minerals is a considerable contributor to carbon dioxide emissions. Government and private investments towards technological advances made by researchers, and improving the regulatory conditions could be robust solutions in our fight against climate change.
Extracting the minerals from more sustainable sources could be another key contributor towards low-carbon mining. For example, extracting lithium from geothermal waters found in Germany and the US has near-zero carbon emissions compared with extracting it from the typical sources, such as hard rock mines in Australia, and underground reservoirs in Chile and Argentina.
Recycling, reuse, and repurposing
Recycling end-of-life batteries to recover precious minerals seems a straightforward solution to reduce the need for mining, but it’s not. The first step in the recycling roadmap should be the efficient collection of used batteries. Li-ion batteries are mainly built into devices that are hard to dismantle.
Further, most of the time, the device is too valuable to be discarded by the user, and likely to be sold for other purposes.
Last but not least, large-sized Li-ion batteries that are used to power cars are still too good to be recycled after they reach the end of their lives. These batteries could be reused in other large-scale applications such as renewable energy storage.
Recycling, reuse and repurposing of used batteries is still in its infancy. More incentives, more study, and perhaps rethinking the design of the batteries is needed to make these strategies effective and economical.
Greener electrodes and battery technologies
The environmental cost of rechargeable batteries could be reduced by investing more in sustainable electrode materials for Li-ion batteries, or entirely new battery chemistries.
For example, many battery manufacturers are working towards packing more and more widely-available silicon in the negative electrode of Li-ion batteries, taking graphite off the table.
Read more: Batteries made with sulphur could be cheaper, greener and hold more energy
In a more recent development – perhaps a game-changer – Tesla announced it will be switching the positive electrode for all standard-range Models 3 and Y, from the high-energy density NCA (nickel manganese cobalt) to the lower-energy-density LFP (lithium iron phosphate).
LFP is an older and cheaper electrode chemistry that, despite having lower storage capacity, offers extended durability and higher safety. Moreover, the use of naturally-abundant iron means reducing the need for nickel and cobalt mining.
Investing in entirely new and potentially greener chemistries such as lithium-sulfur batteries or sodium-ion batteries could be another game-changer in reducing the carbon footprint of Li-ion batteries. Now, such emerging technologies will not be substitutes for Li-ion, but are more akin to supporting technologies to lessen the burden of critical minerals used in today’s batteries.
Climate change isn’t just a threat, it’s an emergency we’re deep into, and lower-carbon batteries are needed to supercharge the fight.